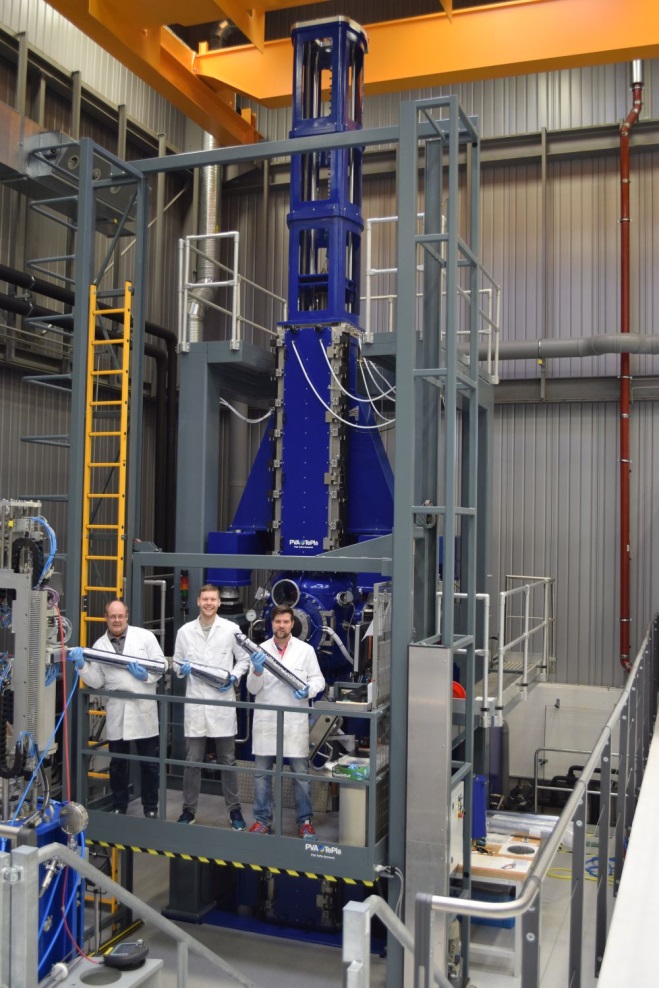
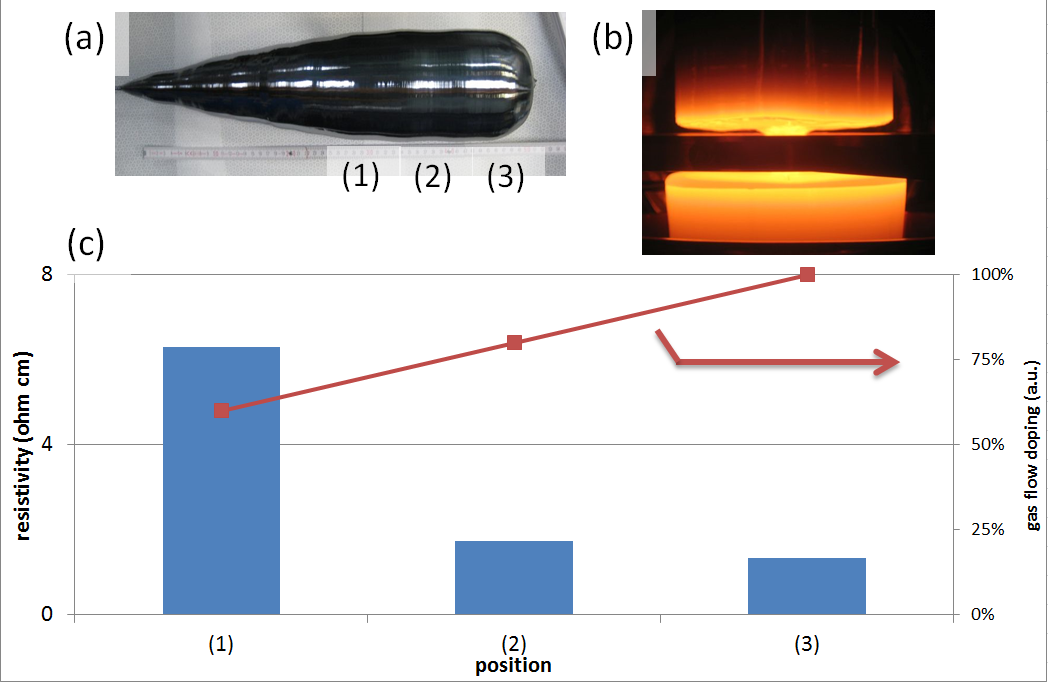
After silicon photovoltaics had relied on simple standard processes for a long time, a sustainable trend toward an upgrade of existing production lines with new technologies now prevail. PERC cell structures and n-type mono Si materials are now establishing themselves.
The next step toward manufacturing methods for high-efficient and low-cost solar cells must therefore be based on crystallization and sawing methods for mono Si n-type materials of the highest purity and a solar-cell structure which profits especially from highly pure material. The Crystallization group at the Fraunhofer CSP is concerned with related issues in the scope of project »Cost-optimized high efficiency solar cells of oxygen-poor n-type mono silicon for industrial mass production« (KosmoS).
The float-zone (FZ method is the production method which yields most homogeneous crystals and wafers of the highest quality. The oxygen concentration in FZ ingots, for example, ranges two orders of magnitude below ingots pulled by Czochralski. In addition, the FZ technology is the method which has the lowest consumption of resources as far as energy, process gas and consumables are concerned. However, since the standard substrate size for solar cells has been a 156 mm-edge length for some time, crystals possessing a diameter of 8'' (200 mm) are needed for this application. Only insufficient process knowhow is available for FZ crystals of this size, for which reason only very few companies worldwide are able to fulfill this requirement.
Important milestones of the three-year project have already been reached:
Diameter
The objective: The production of 8''-crystals lies at the physical/technical boundary of the float-zone process. Therefore only few companies worldwide dispose of the expertise required to produce such crystals. In the scope of a successive increase of diameters the Fraunhofer CSP was able to reach the first milestone on the way from four to eight inches: the first 6-inch crystal was grown. The diameter in the body zone amounted to 155 mm. The resistance of the <100> crystals amounts to approximately 6 Ωcm (n-type). Service lives of about 7 ms reveal that this is excellent material. The specification required for high-efficiency cells is reached, further processes and analyses are planned.
Gas phase doping
The machinery for in-situ gas doping of crystals during the FZ process was set up here at the institute in December 2015 and put into operation. After initial tests a crystal with differently doped regions could be made. The machinery allows for regulating the amount of doping substance while the process is in progress. This makes it possible to produce material possessing various pre-defined resistance profiles with only one crystallization, for example, for various applications or questions to be solved. In industrial manufacturing this type of doping enables an exact adjustment of doping substance concentration, which means a homogeneous lateral resistance profile despite a low segregation coefficient, particularly as far as n-type material is concerned.
The project »KosmoS« is funded by the German Federal Ministry of Education and Research, funding code 02E2-41V7204.